Als onderdeel van het consortium FourCare bouwde Unica de afgelopen jaren mee aan het duurzaamste ziekenhuisgebouw van West-Europa. Dankzij enkele slimme ideeën van Unica boekte het Radboudumc in Nijmegen extra duurzaamheidswinst. “Unica is meer dan een traditionele installateur. We gaan graag een stap verder om klanten te helpen met het realiseren van hun duurzaamheidsambities.”
Bij het Radboudumc in Nijmegen draait alles om gezondheid en duurzaamheid. Op het dak van het nieuwe academisch ziekenhuis liggen zonnepanelen en in de kelder staat een warmtekoude-opslaginstallatie (wko). Het gebouw laat veel daglicht binnen en de muren hangen vol met mos en planten. Patiënten liggen op eenpersoonskamers en kunnen met een iPad alles in de kamer bedienen en maaltijden bestellen. De kantines in het ziekenhuis serveren alleen nog maar gezonde voeding – geen alcohol en minder vlees. Ook qua organisatie bepaalt duurzaamheid de koers. Zo hebben verpleegkundigen meer zeggenschap gekregen en stapt het personeel voor congressen of werkbezoeken op minder dan 700 kilometer afstand niet meer in het vliegtuig.
Ambitieuze planning
Guido de Ruiter, projectleider zwakstroom bij Unica Building Projects, kijkt met een goed gevoel terug op de vier jaar die hij zelf – samen met zijn collega’s – aan het nieuwe ziekenhuis werkte. “Het was hard werken, maar ik ben trots op wat er staat. Het is ook heel gaaf dat we als Unica de kans hebben gekregen om te laten zien wat we kunnen als het gaat om het verduurzamen van gebouwen. Ik ben zelf altijd wel in voor nieuwe dingen en het Radboudumc bleek hiervoor open te staan.”
Een van die nieuwe ideeën werd ingegeven door de relatief korte bouwtijd. Guido: “Om de ambitieuze planning te kunnen halen, besloten we een aantal versnellingstechnieken toe te passen. Normaal gesproken gaan onze monteurs pas aan het werk als de aannemer klaar is met het gebouw. De kabels voor zwakstroom, regeltechniek en soms ook data worden dan draadje voor draadje van haspels afgerold en op de juiste plek gehangen. Voor dit project zijn we al eerder – in de ruwbouwfase – van start gegaan en hebben we voor het eerst gebruik gemaakt van kabelbundels.”
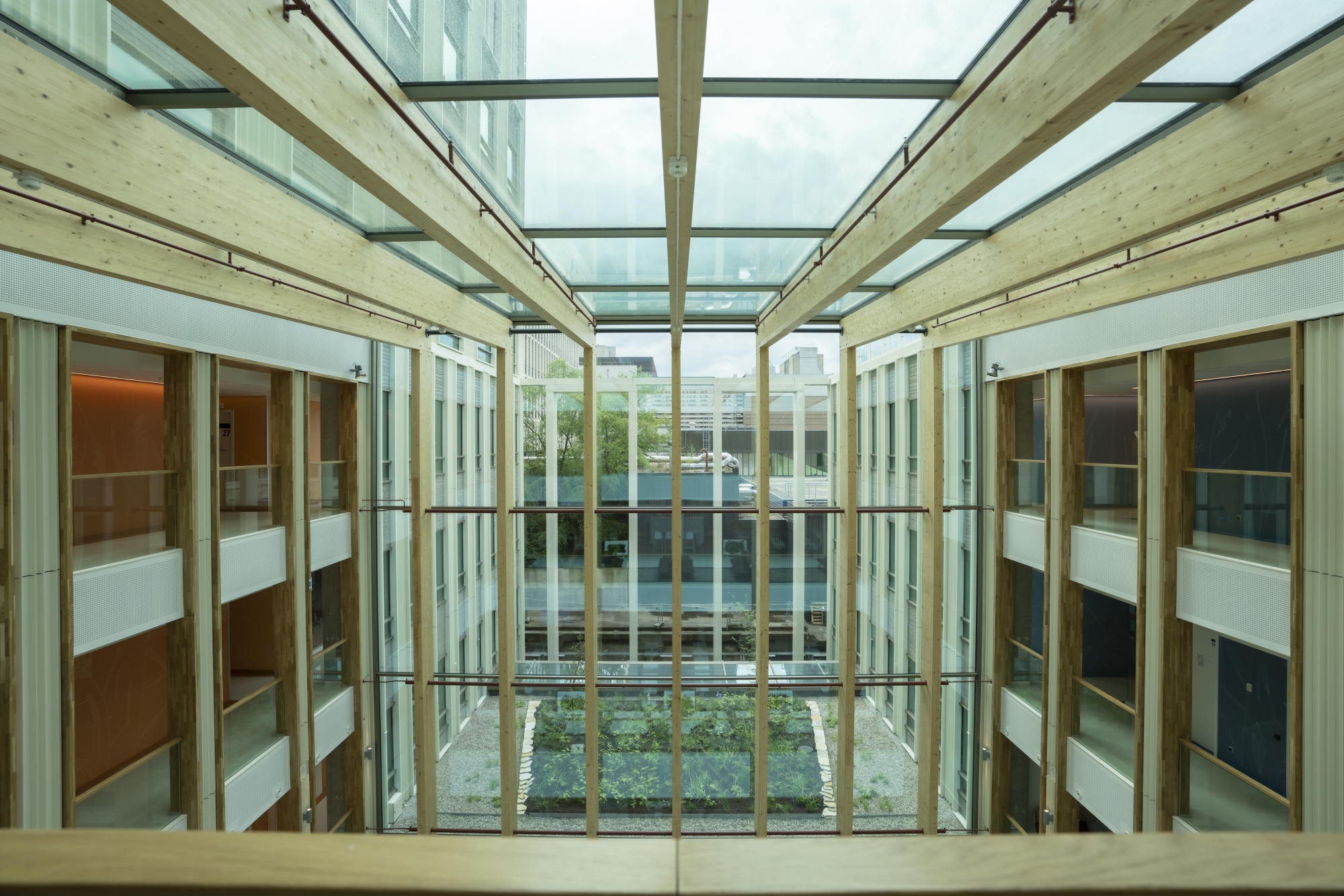
Kabelbundels en prefab
In de auto-industrie en retail wordt al langer gewerkt met kabelbundels, waarbij alle bekabeling exact op maat wordt gesneden en vervolgens samengebonden wordt aangebracht. Guido: “We hebben een 3D-model gemaakt van alle kabels in het ziekenhuis en naar een leverancier van kabelbundels gestuurd. Die heeft het model ingeladen in een machine, die onder de juiste condities kabelbundels produceert. De kabelbundels werden vervolgens in één keer op de bouw aangeleverd, zodat we ze alleen nog maar op de juiste plek hoefden te leggen. Ook hebben we voor dit project meer dan anders gebruikgemaakt van prefab en stekerbare componenten.”
Volgens Guido is dit een bijzonder slimme en efficiënte manier van werken gebleken. “Normaal gesproken heb je wel 20 elektrotechnici nodig om alle verschillende kabels langs zo’n 10.000 knooppunten te leggen. Dankzij de kabelbundels, die zijn uitgerust met duidelijke labels, waren er veel minder vakmensen nodig om de klus te klaren. Iedereen die een tekening kan lezen, kan deze werkzaamheden in principe uitvoeren. Dat biedt perspectief voor de toekomst, waarin de vraag naar technisch personeel naar verwachting alleen maar zal toenemen.”
Duurzaamheidswinst
Kabelgoten, prefab en stekerbare onderdelen. Voor een leek lijken het eenvoudige aanpassingen, maar volgens Guido is de duurzaamheidswinst enorm. “Normaal gesproken heb je veel versnit (deel van het materiaal dat verloren gaat omdat niet het geheel kan worden gebruikt, red.) bij het leggen van kabels. Je probeert zo goed mogelijk in te schatten hoeveel lengte je nodig hebt, maar neemt toch altijd wat ‘overlengte’ voor de zekerheid. Al die restjes – samen een enorme kabelberg – worden weggegooid. Een machine kan dat veel preciezer en zonder onnodige verspilling.”
Het leggen van kabelbundels gaat ook veel sneller. “Waar we normaal 3 à 4 weken bezig zijn met een verdieping, lagen alle zwakstroomonderdelen er nu binnen een week in”, zegt Guido. “En dat heeft natuurlijk een direct positief effect op het aantal verkeersbewegingen. Normaal gesproken rijden busjes van monteurs en leveranciers af en aan. Dat was bij dit project veel minder en heeft het Radboudumc een enorme CO2-besparing opgeleverd.”
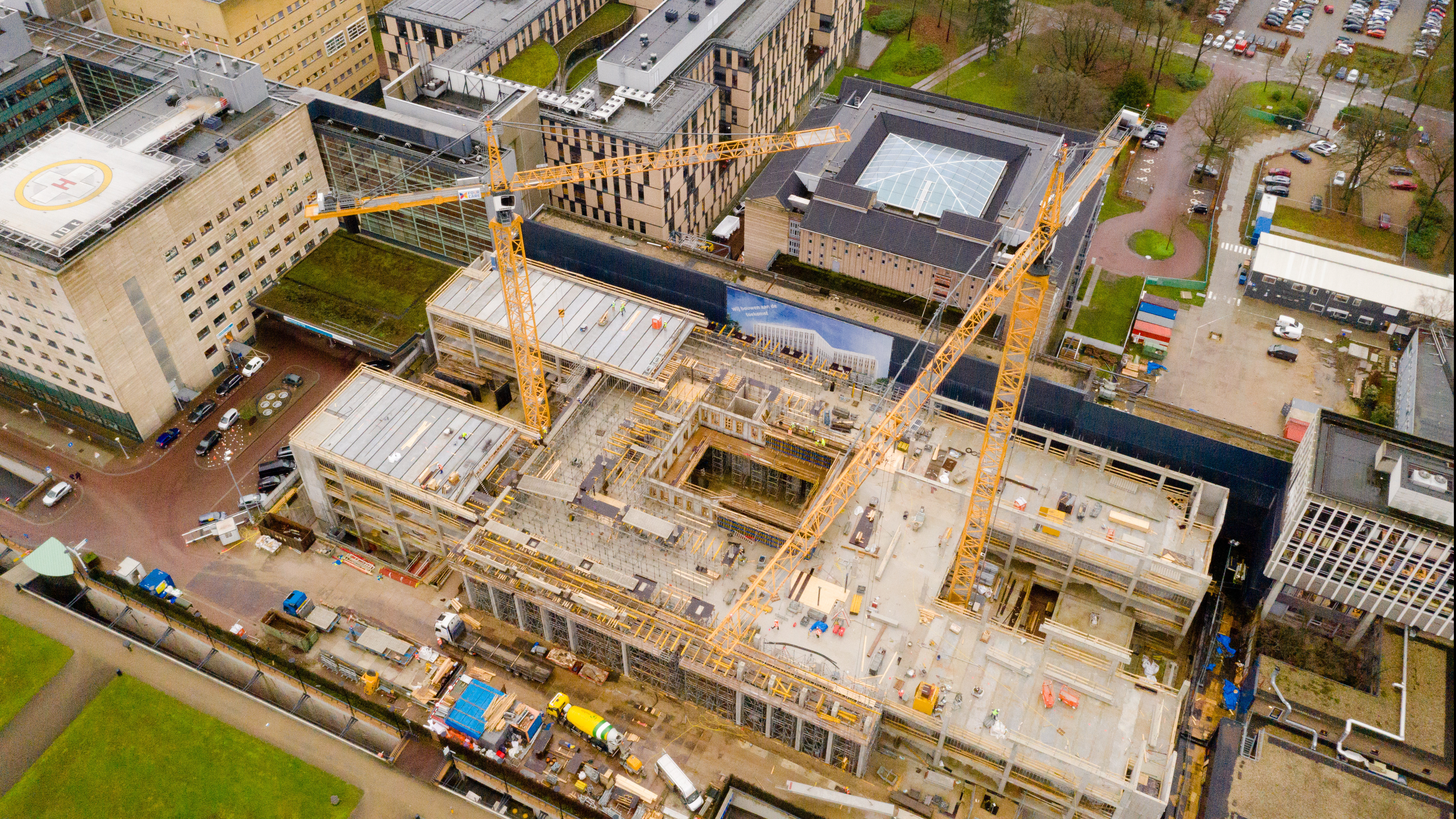
Andere mindset
Waren er dan helemaal geen uitdagingen bij dit project? “Natuurlijk wel”, zegt Guido. “We moesten de klant overtuigen dat deze manier van werken niet ten koste zou gaan van de kwaliteit, veiligheid en continuïteit. Ook intern vroeg dit project om een andere mindset. De jongere collega’s waren meteen enthousiast. Bij Unica werken ook veel vakmensen die hun werk al jaren op dezelfde manier doen en iets hadden van ‘eerst zien, dan geloven’. We hebben daarom eerst een testbundel gedaan en daar met z’n allen bijgestaan. Ook hebben we gedurende het traject alles steeds uitvoerig gecontroleerd en getest. De sceptici waren overstag toen ze zagen hoe degelijk de materialen zijn en hoe snel en gemakkelijk je kunt controleren of alle kabels op de goede plek liggen. Uiteraard zijn er dingen die we de volgende keer anders zouden doen, maar ik sta voor 100% achter ons werk. En ik verwacht dat meer klanten geïnteresseerd zijn in deze nieuwe, duurzame manier van werken.”
